KONUX
AI-powered predictive maintenance for smarter, more reliable railways.
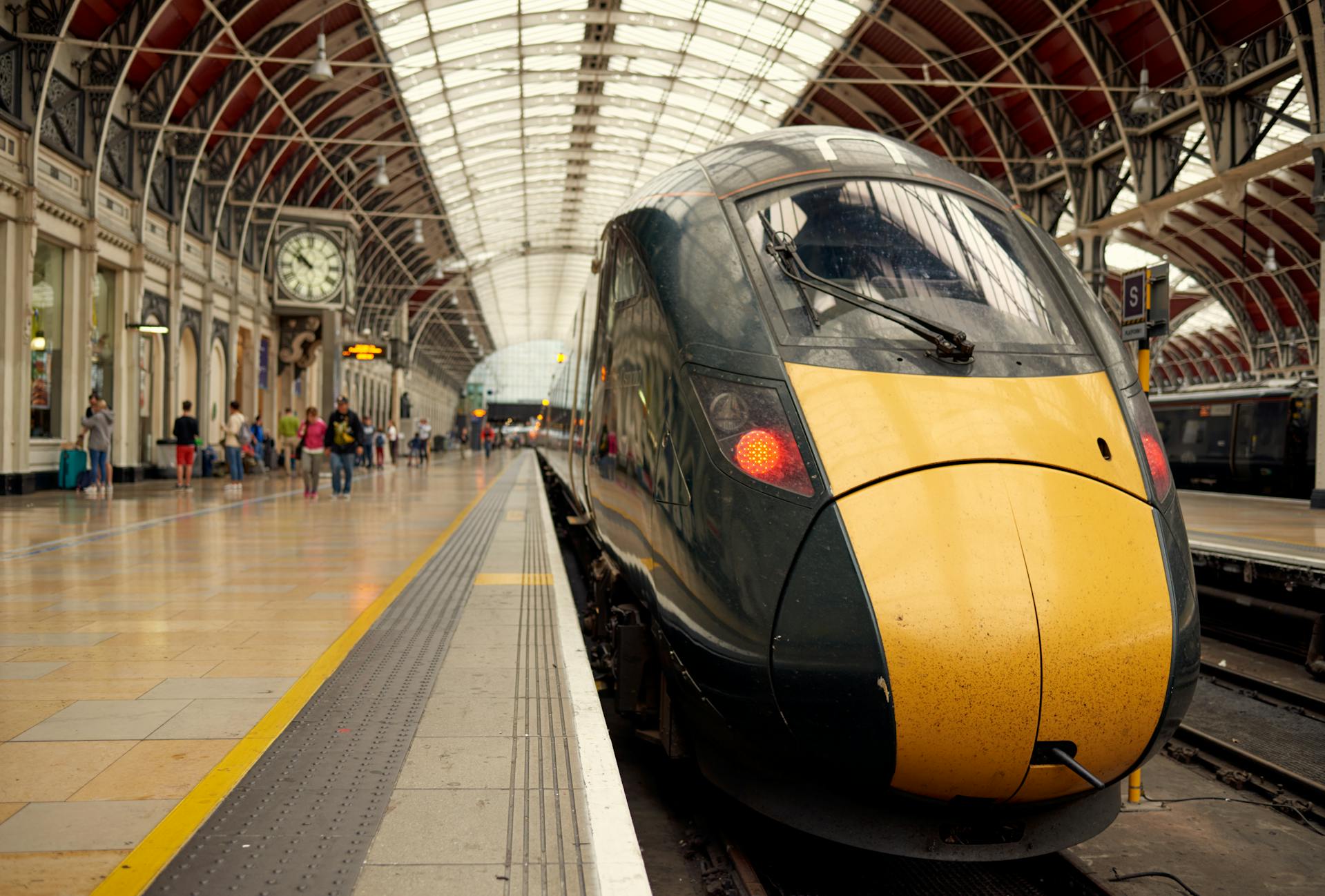




KONUX is headquartered in Munich, Germany, at Flößergasse 2. The company has a international footprint, serving clients across Europe, including major rail operators like Deutsche Bahn and Network Rail.
Founding Story
KONUX was founded in 2014 by four students from the Technical University of Munich—Andreas Loy (then Kunze), Dennis Humhal, Maximilian Hasler, and Vlad Lata. United by a vision to revolutionize industrial maintenance, they combined their expertise in AI and sensor technology to create solutions that enhance the availability and reliability of industrial facilities through predictive maintenance.
Point of Discovery
During a university workshop, the founders identified the potential of integrating smart sensors with AI analytics to monitor and predict the health of critical infrastructure components. Recognizing the challenges faced by the railway industry, they focused their efforts on developing solutions for rail switches and crossings, aiming to prevent failures and optimize maintenance schedules.
Initial Success
KONUX's innovative approach quickly gained traction, leading to a $2 million seed investment from Silicon Valley investors, including Michael Baum and Andreas von Bechtolsheim. Their technology was soon adopted by Deutsche Bahn, Germany's national railway company, to monitor high-speed network switches, marking a significant milestone in the company's early growth.
Breakthrough Moments
In 2020, KONUX secured a landmark contract with Deutsche Bahn to digitize over 650 switches, later expanding to 3,500 assets by 2023. This project represented Deutsche Bahn's first cloud-based SaaS infrastructure initiative, solidifying KONUX's position as a leader in AI-driven railway maintenance solutions.
KONUX's core technology integrates Industrial Internet of Things (IIoT) devices with advanced AI and machine learning algorithms to provide real-time monitoring and predictive analytics for railway infrastructure. Their flagship product, KONUX Switch, continuously assesses the condition of key switch components, enabling proactive maintenance and reducing unplanned downtime.
Impact to Date
KONUX has revolutionized railway maintenance by reducing costs, enhancing reliability, and increasing network capacity through AI-driven predictive solutions.
Impact Use Case #1:
Deutsche Bahn – Enhancing Switch Reliability
KONUX partnered with Deutsche Bahn to monitor thousands of high-speed rail switches, a key source of system failures and delays. With KONUX’s smart sensors and AI-driven insights, Deutsche Bahn transitioned from reactive to predictive maintenance. This shift led to a 25% reduction in maintenance costs and significantly fewer service disruptions. It also marked Deutsche Bahn’s first major move into cloud-based SaaS infrastructure, setting a new standard for digital rail operations in Germany.
Impact Use Case #2:
Network Rail – Optimizing Maintenance on Sussex Route
To address recurring switch failures on the high-traffic Sussex route, Network Rail adopted KONUX’s predictive maintenance platform. The system provided continuous monitoring and forward-looking analytics, helping the team prevent breakdowns and optimize service schedules. With fewer emergency interventions and better planning, Network Rail improved route reliability across one of the UK’s most heavily traveled corridors.
Impact Use Case #3:
Infrabel – Reducing Tamping Costs
Infrabel used KONUX to improve trackbed maintenance, focusing on tamping—an expensive and often inefficient process. By monitoring real-time ground and geometry data, Infrabel shifted to a data-driven approach that reduced unnecessary work and cut tamping costs by up to 66%. This allowed for smarter interventions without compromising safety or performance.
Impact Use Case #4:
Oc’Via Maintenance – Enhancing Geometry Monitoring
Oc’Via Maintenance adopted KONUX to improve how it monitors and maintains track geometry along a major high-speed rail line. KONUX’s sensors and AI delivered ongoing insights into track wear, enabling more precise and timely maintenance. This reduced operational disruptions, extended infrastructure lifespan, and supported safer, smoother high-speed travel.
